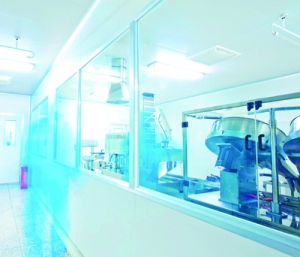
BioPharm: In implementing a QbD approach, what would you identify as the critical quality attributes (CQAs) in sterile manufacturing and aseptic processing?
Weikmann: The potential critical quality attributes of a customer’s drug product in terms of aseptic processing are determined by the nature of the product and by the definition of its target product profile. Most common identified critical attributes refer to physical, chemical, and microbiological properties. We recognize sterility, bacterial endotoxin, and dose accuracy as three of the essential CQAs.
Equipment Design and Operation
BioPharm: How is equipment design and operation modified when implementing QbD in sterile and aseptic manufacturing?
Weikmann: Looking first at equipment design, we feel strongly that the design review process has to be mentioned as an essential tool. Design review is a decisive milestone within the development process for a single piece of equipment. It is performed through the adjustment of an initially created design with its particular requirements. This is important to control the results of the former activities, as well as to identify and solve any existing problems prior to the start of the drug-manufacturing process. We primarily execute a design review within the construction phase for each cGMP relevant piece of major process equipment. An example element of this design review is conducting mock-up studies.
Looking at the operations side, serving multiple customers with different product and process specific requirements, our equipment has to be set-up highly flexible. Such an arrangement offers the benefit that, based on the product specific requirements as well as based on the performed pump studies within the QbD approach, the specific equipment components, such as the most adequate product and process-fitting filling pumps, can be used right away for subsequent production.
Challenges in implementing QbD
BioPharm: What are the challenges in applying QbD in sterile manufacturing?
Weikmann: In our experience, the main challenges in applying a QbD approach are due to the intensity of time, cost, and resources in the early-development stage. Another significant challenge is the high degree of expertise that must be in place to run a proper QbD approach.
Regarding timing, a much longer timetable has to be included. As for costs, the higher costs are due to the variety of additionally performed studies. And higher resource management is due to equipment, different materials as well as staff.
In summation, it is always a product-dependent balancing act between the risks and consequences on one hand, and the cost during the development stage on the other. Even if challenges as previously described appear in the early stages, the gained knowledge will likely result in an economic benefit in the long-term commercial lifecycle.
Benefits of QbD
BioPharm: What additional understanding is gained through a QbD approach compared to a traditional approach?
Weikmann: The most important understanding gained by running an operation through a QbD approach versus the more traditional approach is to realize the necessary requirements of a customer´s product already in an early-development stage to accommodate the product target profile. These requirements are not limited to product quality only. They include the process performance as well as the applied systems and the environment, for example, optimized and reduced lyophilization process cycles.
Based on various studies, differing possible cases are evaluated in detail. This examination ultimately leads to a better understanding of the process variations, thus resulting in an acceptable design space. Consequently, using a QbD approach offers the possibility of gaining better process knowledge, resulting in an improved robustness of the entire process.
BioPharm: How does QbD improve quality assurance and how can it mitigate problems in manufacturing?
Weikmann: Through a greater importance given to process development activities and the resulting large number of development studies performed within a QbD approach, a better process understanding is gained. Within the risk-management approach, risks are already identified in an early stage. Consequently, risk mitigation activities can be developed, and a risk-based control strategy implemented from the very beginning of the commercial stage, forming the basis for improvement of quality assurance and quality oversight.
BioPharm: How is technology transfer improved under a QbD approach?
Weikmann: Technology transfer indeed is one area that is especially improved through a QbD approach. It leads to improved possibilities to monitor and evaluate the process. Becoming familiar with a drug product´s frame and its limits through conducting numerous tech runs of varying versions allows one to define the product´s specification in which the process is running robustly.
A day-to-day business example to showcase the improvement of tech transfer through QbD for customers is by demonstrating the lyophilization cycle development of a customer’s product. For example, by using a QbD approach with gaining the corresponding data based on numerous performed lyophilization tests, we realized a significant reduction of the lyophilization cycle for a particular customer product. This reduction resulted in saving the customer a high amount of capital, primarily within the large-scale commercial production.